WE ARE HAPPY TO SEE YOUR SHINING FACE
When your products reached ON TIME!
BIG SAVINGS on Sourcing Cost!
QUALITY Better than Past!
Customer Complaint ZERO!
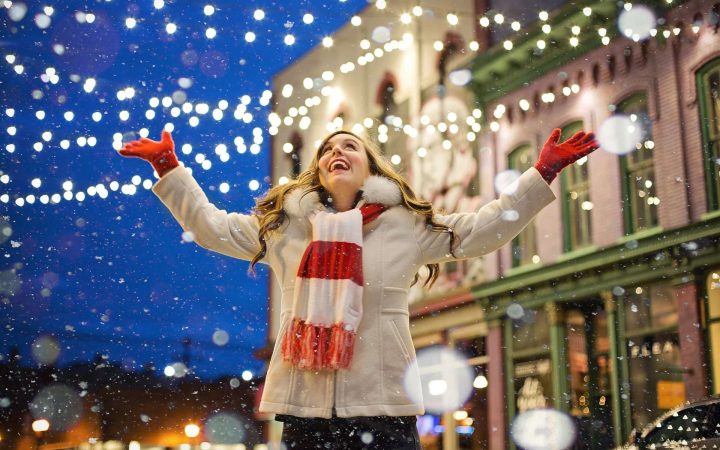
The is conducted before production starts at Supplier’s facility. It is usually done to crosscheck for final verification of bulk fabric, trims, raw materials/accessories, styling cutting way, cut, components, workmanship of the garment, pre-production sample, manufacturing details including production areas etc.
Our Inspectors will verify the availability and condition of materials, material’s in transition, review manufacturer’s plan for production and confirm equipment availability.
This inspection helps to ensure that supplier is ready to start production on time and meet the production deadlines. It also helps to identify any quality risks before commencement of mass production.
Key Checkpoints;
- Material conditions including ordered and received quantity.
- Conditions of bulk fabric, trims, raw materials/accessories, materials in transition, styling cutting way, cut, components, workmanship of the garment, pre-production sample, manufacturing details including production areas etc.
- Workmanship of materials and components
- Production readiness
- Equipment maintenance and availability
Fabric inspection is considered as pre- production inspection for garments or other textile products. It is very important to ensure the quantity and quality of the key materials of production like Fabric. This process is a preventive one that could be broadly defined as the process of determining if a product deviates from a given set of specifications.
It helps to identify the defects of fabrics to lower the risk of product rejection in later production stage. Generally, we use 4-point system to check fabric quality. QIV provide Fabric Inspection Services through visual, automated or online.
Quality inspection of garments or fabrics can be done by maintaining four systems. Although there are 4 methods of fabric inspection, but 4 point system is the most popular method to conduct fabric inspection.
Methods of the Fabric Inspections:
- 4 point system
- 10 point system
- Granville “78” System
- Dallas system
Inline Inspection is done at the start of production where a first batch of garments is inspected. It provides additional assurance of quality and provides a more transparent view of on-going production status by looking into the quality of semi-finished or final products and production lines.
It helps to take immediate action in possible discrepancies/variations and to make necessary corrections or adjustment to be made bulk production. IPI ensures better estimate the overall production and bring more improvement in the production with insightful Corrective Action Plans which developed by our experienced inspectors and endorsed by factory’s production experts.
QIV also recommend a follow up Inline Production Inspection is an ideal idea to ensure initial discrepancies have been corrected and rectified. This inspection is generally carried out when discrepancies have been detected during initial production inspection. However, this follow up is not necessary in case of having plan to conduct “During Production Inspection (DPI)”
Key Checkpoints;
- Bar Verifications
- Carton shipping mark Check
- Product packaging and packing Check.
- Product Assortment Check
- Color shade variation Check
- Rub Check by Water and Dry
- Product safety Check (Button, Zipper, Draw cord, Needle detection, Moisture GSM &Others)
- Product fitting Check (Measurement and Dummy)
During Production Inspection (DPI) is normally performed at 8 to 15 percent of the finished goods to ensure that any initial discrepancies/variations have been rectified. This inspection is a follow-up to the initial production check and ensure smooth production. Beside checking of the initial products coming off the line in a manner consistent with our pre-shipment inspection techniques, it also verifies and document the status of raw materials, components, and partially finished goods.
We use ANSI/ASQC Z1.4 (ISO 2859) to verify that your production run properly, you will be receiving your products as matching the samples you approved. Inspector will check the finished and semi-finished goods. Inspector will also point out possible defects during production. Our Inspection Report containing information about production flow, equipment use, production capacity and any potential issues in an easy format. This helps to find out possible defects and make rectifications at earlier production stage.
More DPIs can be conducted at different stages along the production period depending on complexity of products, production process, order quantity, reliability of the factory, etc.
Key Checkpoints;
- Initiated when the factory has manufactured 15 to 80 percent of the total order quantity
- Rigorous inspection of the initial finished product and raw materials, components and partially finished goods
- Gain early knowledge of potential quality issues
- Production status and capacity
- Workmanship
- Dimensions and weights
- On-site function and safety testing
When an order fails in pre-shipment inspection, defect sorting is sometimes used as a substitute for pre-shipment inspection of high-value products. Before shipment, QIV’s inspectors check the entire batch of finished goods according to your specified inspection check points. Then remove any defective goods from the production batch and either rework or destroy them, depending on the severity of the defect.
When quality issues are significant and rework is unfeasible, you may find yourself with a big number of goods that you can’t sell. Substandard items that you are unable to sell can harm your brand’s reputation in the long run. In such instances, QIV’s supervised product destruction may be your best option. We’ll coordinate destruction and oversee the destruction process to safeguard you and your customer.
QIV Production Monitoring will be your right choice if your supplier has failed several stage of inspections for the same reoccurring defects. This service enables you to significantly reduce the number of defective items that are packaged and dispatched. It will definitely save your time and money.
Pre-shipment inspections and production monitoring rarely take a random sample of a completed order. It helps to inspect the products at multiple stage on the assembly line until packaging. When inspectors identify defects, they remove the affected units from the line and segregate them for rework or other corrective action in accordance with your quality requirements.
Key Areas;
- Inspectors stationed on the factory floor throughout production to identify and communicate all defects found to your supplier
- Receive daily reports on order status and quality
- Assess progress on corrective actions
- Production line audit
- Workmanship
- Packaging and labeling
- Dimensions and weights
You might need to collect samples for review, evaluation, lab testing or just to make sure that your supplier correctly understands your requirements
The problem with asking your supplier to send you samples is that it’s hard to be sure the samples are representative. Often a supplier will choose only the best units or those they know will meet requirements. Later you might discover the quality, condition or characteristics of the finished goods you or your customers ultimately receive differ from the sample you collected earlier.
As a third-party independent company, QIV ensures a right sample selection process. Our Inspector will randomly pull samples in the factory. This assures that any sample testing or review results are representative and unbiased.
FRI is carried out when the production of the total quantity of an order or when at least 80% of your order has been export-packed. It’s designed to catch any quality issues with your finished products and packaging before they go into shipping containers. This stage will help you to make shipping decision.
Our inspector pulls a random sample of finished and packed goods, based on internationally recognized statistical random sampling technique AQL (ANSI / ASQ Z1.4-2003) along with industry-standard test results and measures and a percentage of the garments will be inspected.
This percentage usually being stipulated by your requirement. Our inspection verifies whether the material, performance, function, Quantity, workmanship, size specification, etc. and ensure the required product specifications are met as per your requirements or not.
Key Checkpoints;
- Initiated when the factory has manufactured 80 to 100 percent of the total order quantity
- Order quantity check
- Workmanship
- Dimension and weights
- On-site function and safety testing
- Packaging and labeling such as dirt & stains, the correct size of poly bag, garment quantity per carton, etc
- Shade variation from one part of the garment to another, correct labeling etc
Container Loading Supervision is final round inspection which ensures your order is completed and safely loaded in a container before shipment.
It protects you from theft, mishandling and incorrect loading. Our CLS services also cover quantity of goods to be loaded, cleanliness and environmental conditions of the containers will be checked. our inspectors will check packing details and quantity against documentation about at loading and will witness the whole process of loading the goods into the container.
This inspection may conduct in supplier’s factory premises or in the yard of shipping company.
Key Checkpoints;
- Initiated during loading of goods into shipping container
- Container conditions
- Product specifications
- Shipping marks, packaging and labeling
- Shipping documentation
- Quantity loaded
Mold is a fungus, and like all fungi, it thrives in moist places. Mold spreads by emitting spores, microscopic particles often as small as a single cell. Spores float around in the air until they land on a surface. Mold spores are everywhere, outdoors as well as inside your factory. It would be practically impossible to remove all mold spores from a factory without installing some kind of massive industrial clean room filtration system.
Luckily, mold spores only form mold when they land on a moist surface. That means that if you can keep the interior of your factory dry, you can avoid having any problems with mold. The best way to prevent mold in your home is to clean up spills, repair leaks in your roof, plumbing or HVAC system.
- QIV offers consultancy service for Amazon FB inspection process and preparation for conducting FB inspection by 3rd party inspectors who will inspect your goods on the spot before shipped to warehouse of Amazon.
- QIV will guide you about the specific requirements regarding product packaging, shipping packaging and labeling.
- QIV also offer self-reference inspection by quality inspectors who can check on site whether all of these are compliant with the guidelines and thus save possible fines and trouble with Amazon.
- Ensure to meet all quality expectations and applicable regulatory requirements & identify and remove the defective products from the production batch.
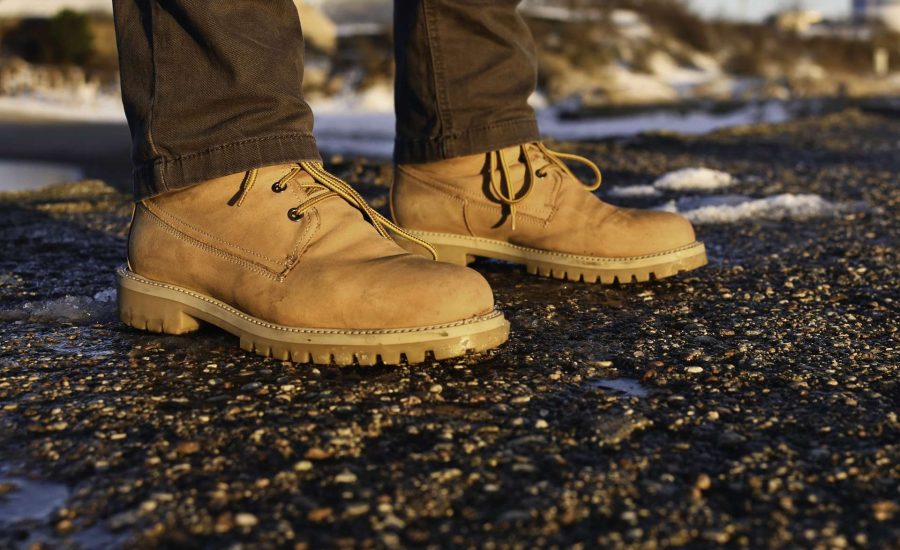
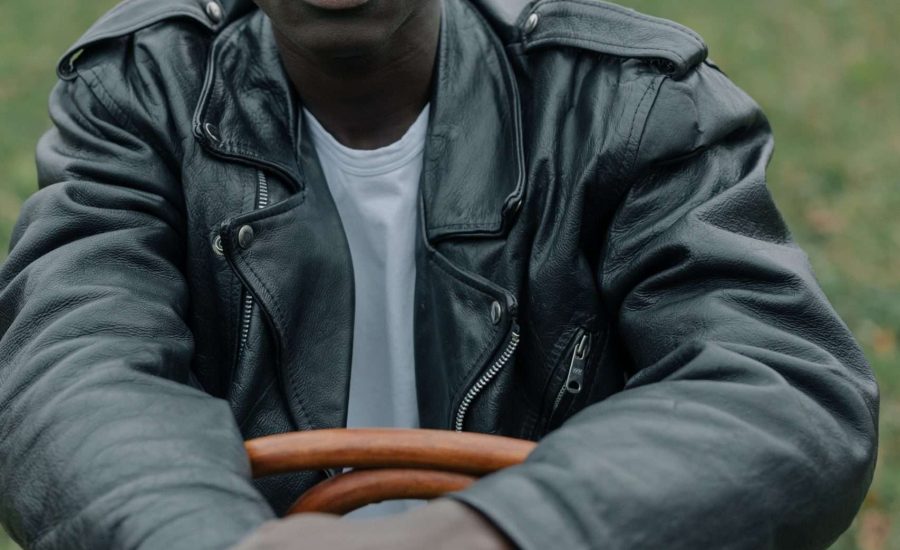
LEATHER & FOOTWEAR INSPECTIONS
Raw Material Inspection
Our Raw Material Inspection service cover; checking the incoming quantity, quality, styles, and other details of raw materials, as well as production equipment, it ensures your production starts in the right place.
Accessories Inspection
QIV provide inspection services for the all kind of accessories of leather, metal, rubber or textile for leather bag, shoe and other leather goods during any time of production or after finish goods.
Pre-Production Inspection
Pre-production inspection takes place before production starts. QIV offers an extensive pre-production inspection for footwear and external components as well as the bags or clothing items. We follow international standards ISO 2859-1 for sampling. Moreover, we offer inspection services for leather roll according to 4 or 10 points method.
QIV offers following Inspections for Leather & Footwear items;
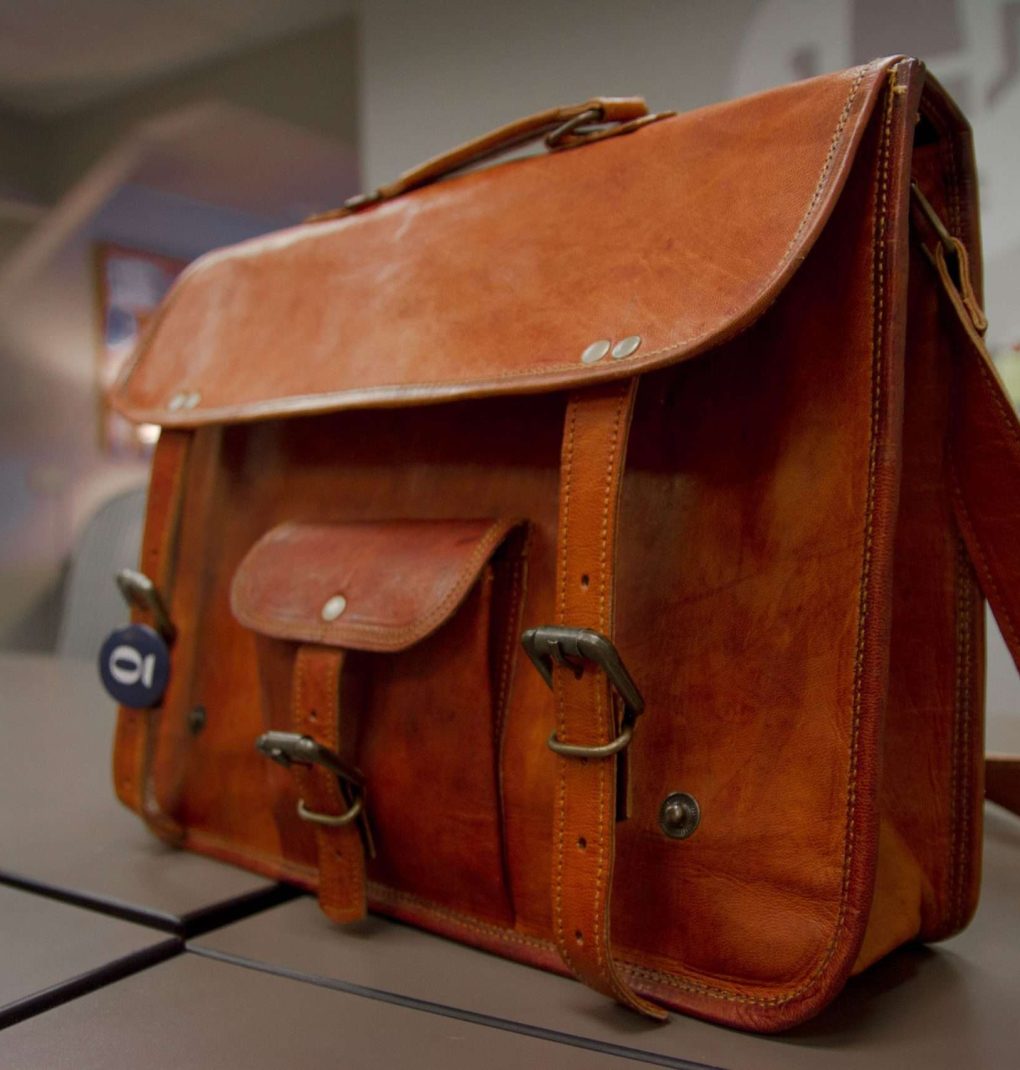
- Initial Production Inspection
- During Production Inspection
- Inline Inspection
- Production Monitoring/Follow up
- Pre-Shipment Inspection
- Pre-Customs Clearance Inspection
- Container Loading Supervision
- Final Inspection
- Defect Sorting
- Mold Inspection

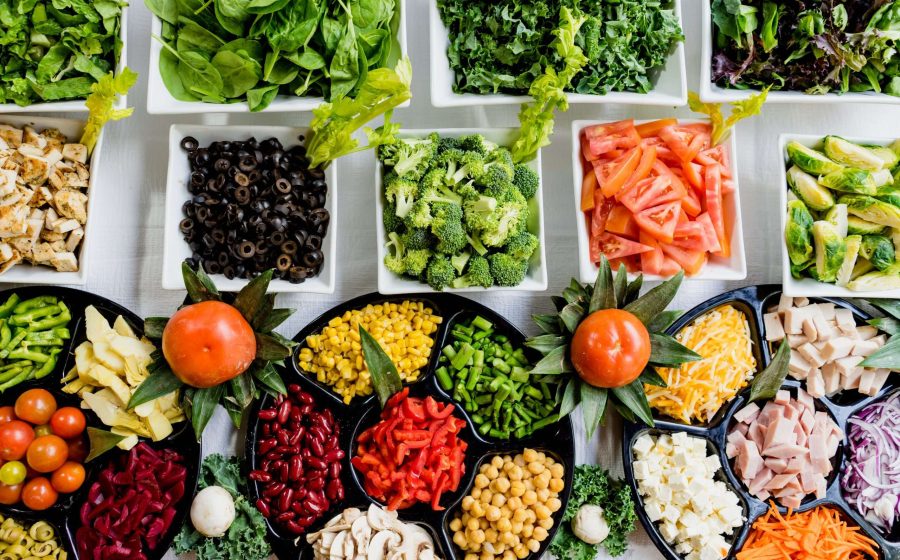
FOOD & AGRI INSPECTION
Agri & Commodity Inspection
QIV offers a wide range of services to help the clients to meet the needs and minimize risks of commodities like shrimp, seafood, rice, wheat, cotton, fertilizer, jute, sugar, tea, potato, seed etc.
QIV Inspection identifies the issues of commodities at their source, maintains product consistency, ensures local and legal regulations are followed during transportation, storage etc align with national & international legislation and COC.
QIV Inspection allows you to control a set number of samples within a defined lot and follow a fixed sampling plan according to specific points of control.
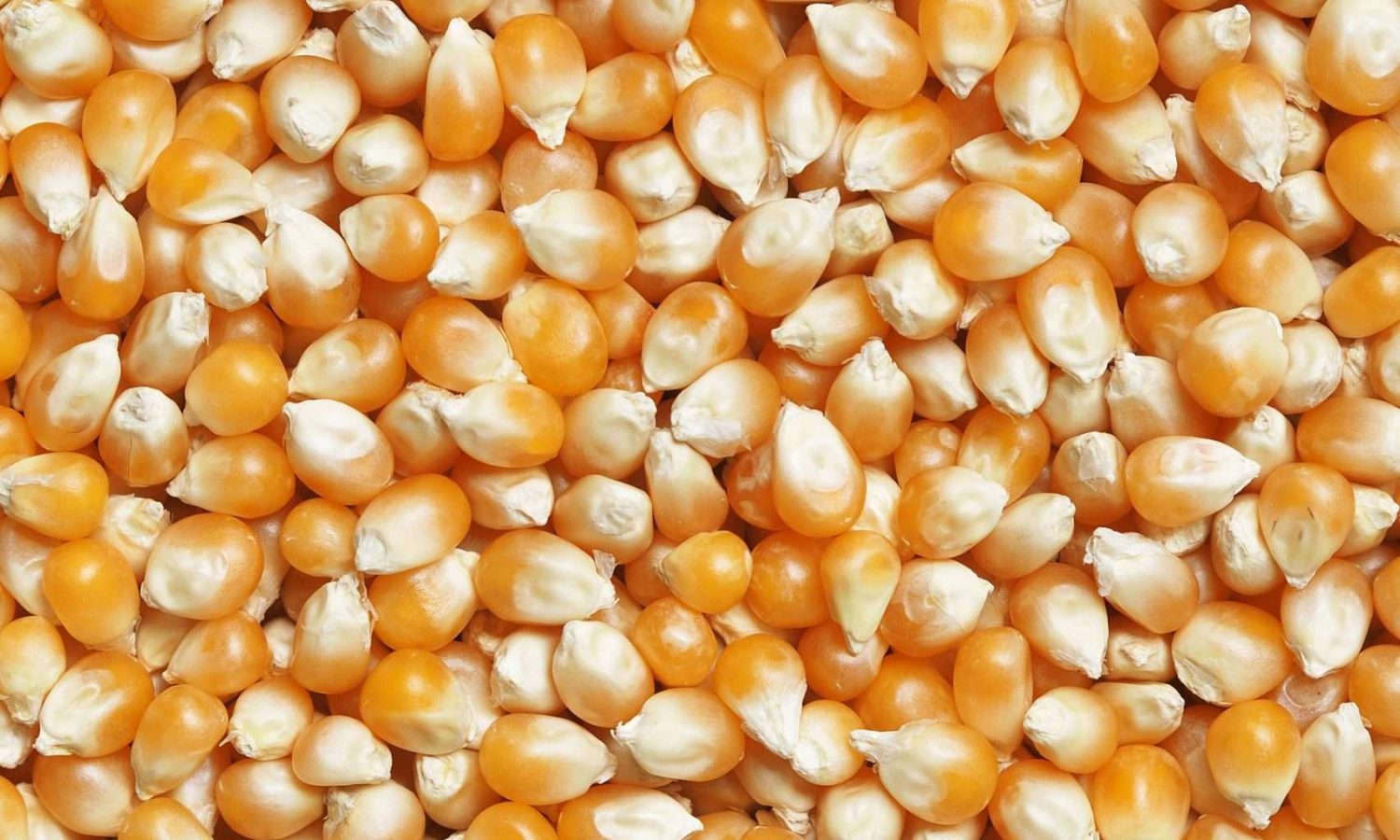
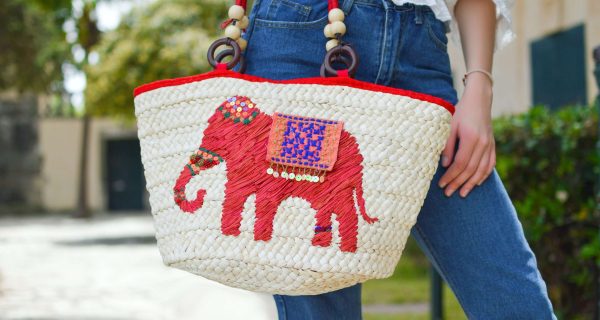
Jute & Jute Products Inspection
QIV offers inspection for raw jute, fabrics, all kinds of jute bag, yarn, jute products, jute rope, jute polybag, Jute Webbing etc. Our inspections cover measurement, weight, weaving, joint, construction, moisture content, hydrocarbon check etc.
Our inspection services help you detect defects as soon as possible, allowing you to make modifications as needed and lowering the cost of product manufacturing and supply disruptions. Our Inspectors keep an eye on every critical point in the supply chain to ensure that all aspects of risk are covered.
Food & Food Packaging Inspection
Food and food items related to packaging are very sensitive. The whole process of food processing requires to have high attention. A single incident or wrong handling can damage company reputation, shipment cancellation, losses of whole shipment cost etc.
Our inspection techniques enable you to develop better food products and food packaging that meet international or national standards. As per various marketing zone and regions, we can help you meet the complex regulatory requirements of health & safety issues.
Our inspectors and experts identify the risks and defects and raise alert to your attention through our services so that you can have precaution before ship the food products.
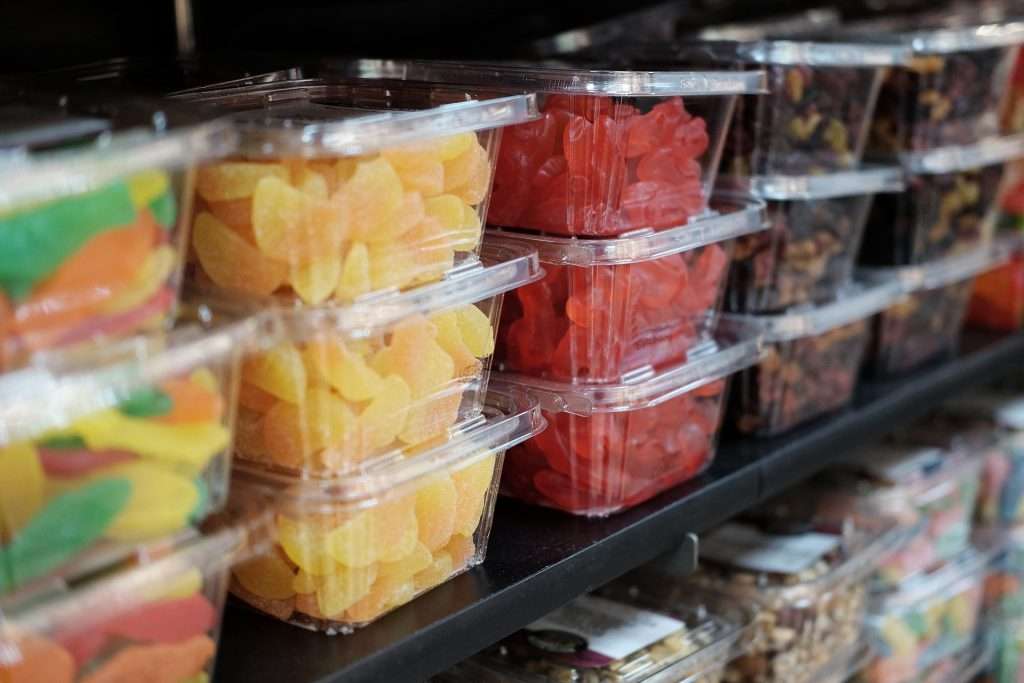
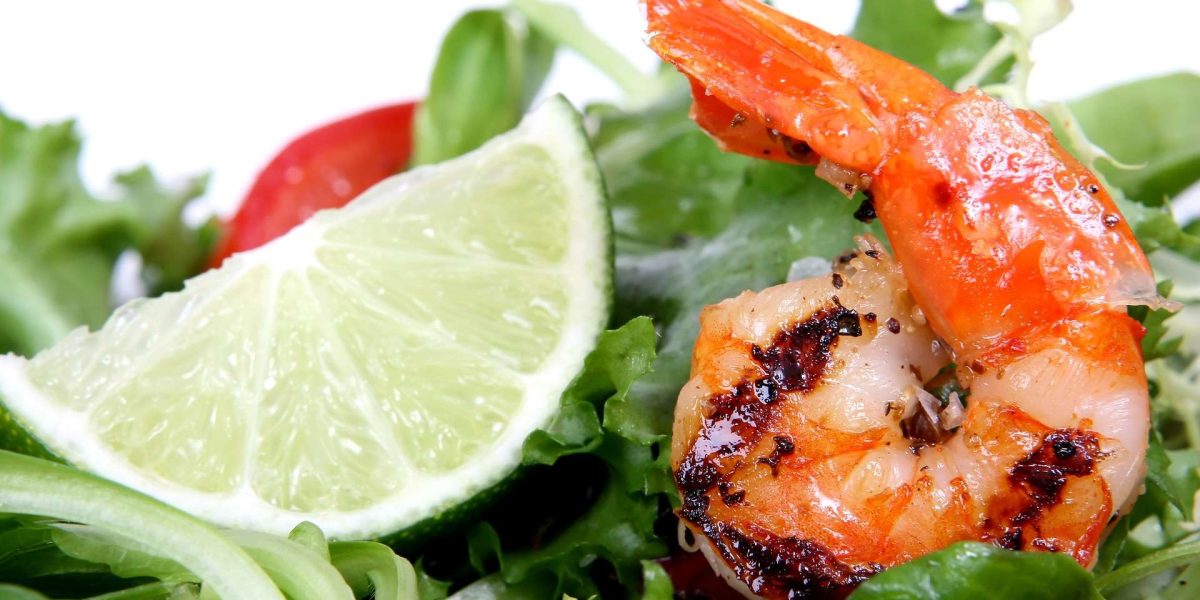

HARD GOODS INSPECTION
QIV offers an extensive range of inspection and verification services on hard goods. Our Inspectors help clients to ensure the hard goods product and their packaging comply with all national and international regulations.
Our services cover quality, safety, performance assurance, risk analysis, defect identification etc.
Our hard goods services include but are not limited to the following products;
- Furniture and wood related products
- Ceramic and glassware
- Bicycle
- Interior decorations, Apartment etc.
- Jewelry and fashion accessories
- Household
- Sports goods
- Batteries, electrical and electronics items
- Promotional Items, Candles and candle accessories
- Artificial hair/wig
- Sea Grass, Areca items
- Clay, bamboo items etc
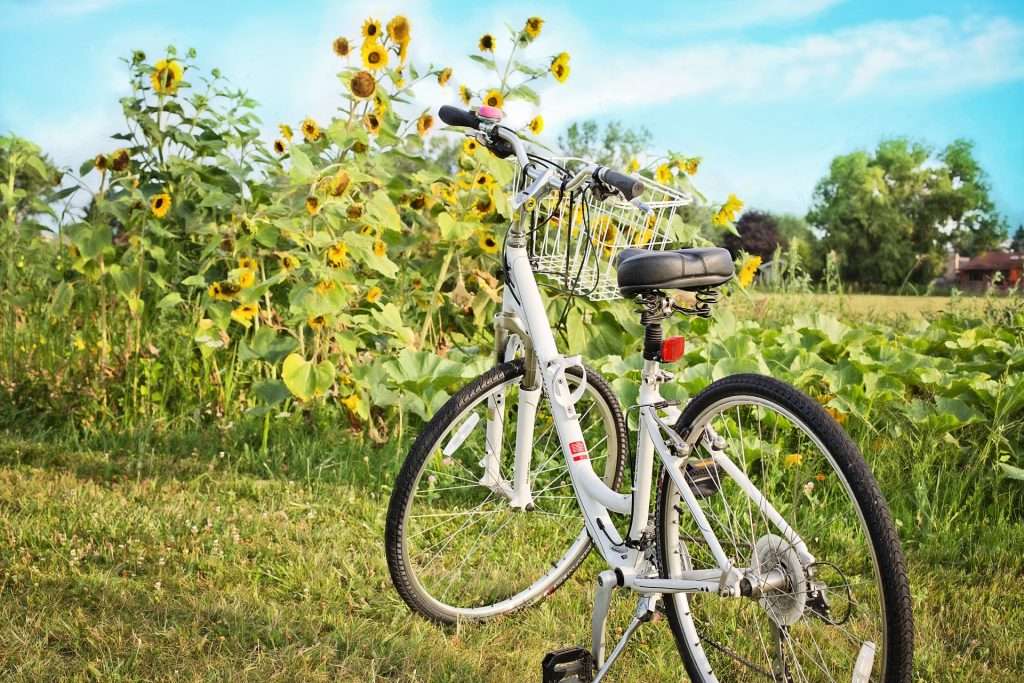
OUR HARDGOODS INSPECTIONS
- Pre-Production Inspection – Ensures raw materials are checked before production so that the risk of non-compliance is minimized and understand the readiness of the production and plan accordingly.
- Initial Production Inspection – This is a visual check of the products and compares the client’s provided specifications, technical drawings and the client’s quality requirements etc.
- During Production Inspection – This inspection cover materials quality, dimensions, and finished products during manufacturing
- Final Random Inspection – During the final random inspection, the inspector will check the product quality and quantity along with product appearance, performance, workmanship etc. Besides, checking packaging, labeling and shipping mark is also an important part of this inspection. The inspection is conducted based on randomly selected finished products.
- Loading Supervision – This supervision ensures that the goods checked via a Final Random Inspection are shipped.
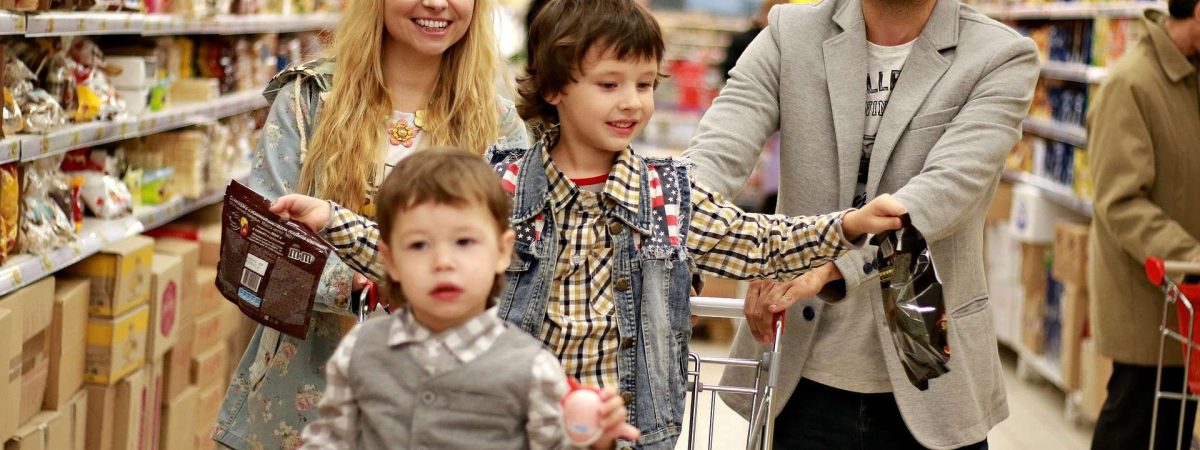
TOYS & CHILDREN’S PRODUCTS</strong)
During the last few years, considering the priority of health & safety in children’s products, the authority of many countries like Australia, Brazil, Canada, China, Russia, and Japan have developed their own toy regulations and standards besides US and EU. We refer to toy standards from destinations such as the USA, EU, Australia, Canada, and Mexico including CPSIA, ASTM F963, EU toys safety directive, IEC, ISO/TC 181, AS/NZS ISO 8124, SOR/2016-168, and NOM-252-SSA1-2011.
Moreover, manufacturers, importers, and retailers involved in children’s toy manufacturing must implement a huge supply chain management process to ensure toy regulations and meet consumer expectations for toy safety.
QIV offers inspection services for toys and children products for many retailers, importers, and manufacturers, ensuring the production process generates juvenile products of consistently high quality and that are safe for children. Our services start from the review of manufacturing facilities to the final shipment stage for juvenile products and baby toys for indoor, outdoor, educational, and imaginative purposes.
Our scope of evaluation/assessment covers the following areas besides product quality inspections services;
• Evaluation of Facilities, Machinery and Production Methods
• Evaluation of Product Designs, Labels, and Packaging
• Assessment of manufacturing process
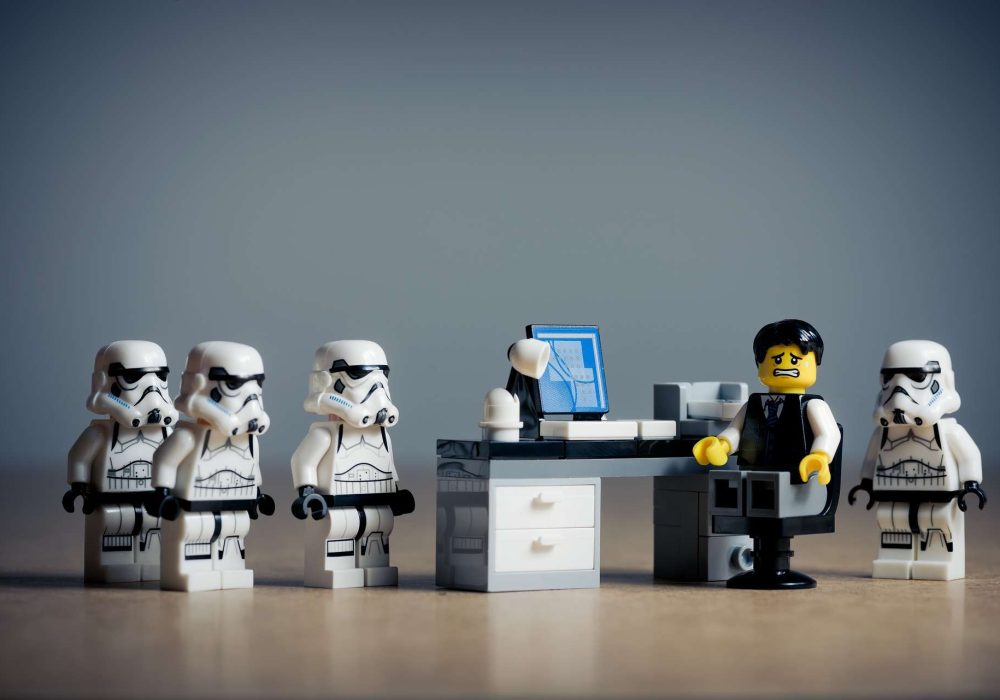
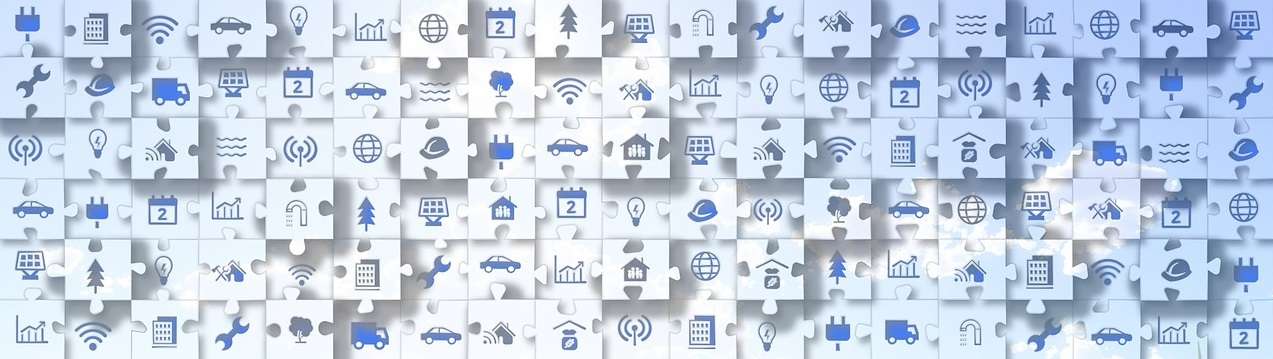
INDUSTRIAL INSPECTIONS
QIV offers inspection services in various heavy industrial segments including but not limited to Power & Renewable Energy, Steel, Cement, Oil & Gas, Chemicals, Process Industries, Automobiles, Electronics etc
In most of the cases during our Inspection, the following key points are included;
- Document Review & Verification
- Material identification
- Visual examination & dimentional inspection
- NDT & Proof Testing (if require) through special arrangement.
- Integrated Inspection Report
- Crane & Lifting Inspection
- Loos Lifting Gear, Lifting Equipment & Lifting Equipment Management
- Electrical Inspection
- Generator, Boiler & Chimney
- API, Pipeline
- Fabrication inspection
- Welding supervision and monitoring
- Vehicle, Machineries & Equipment Inspection
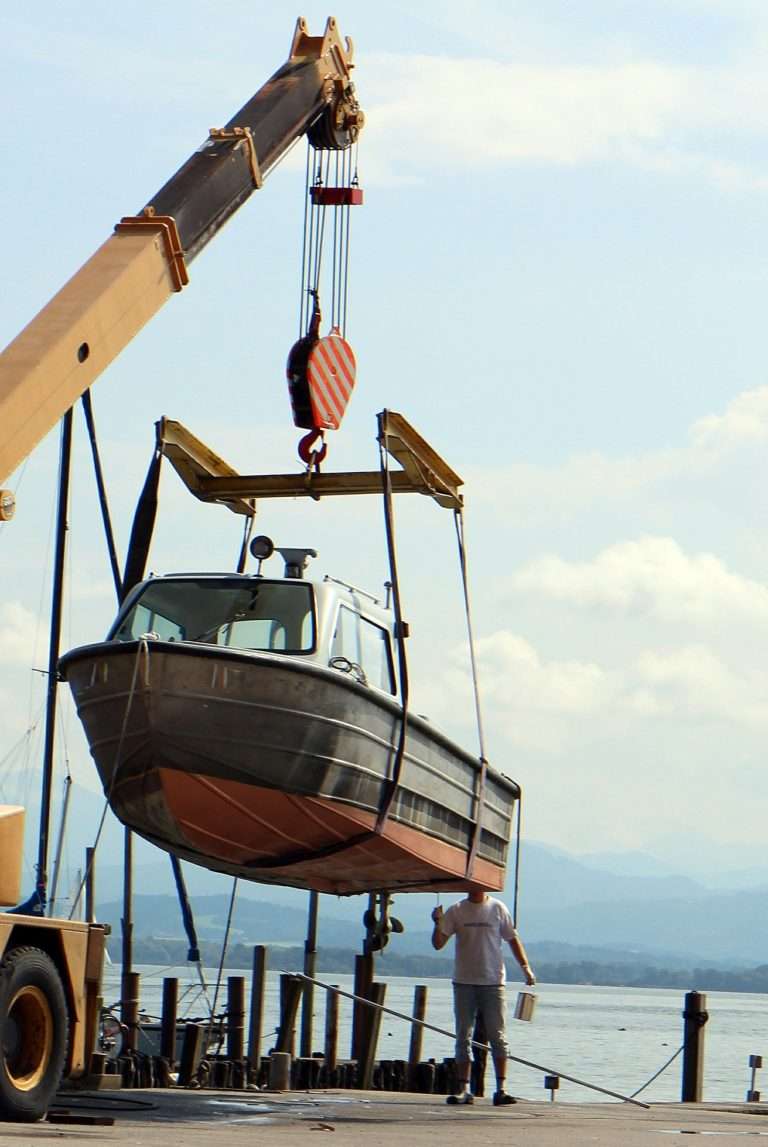
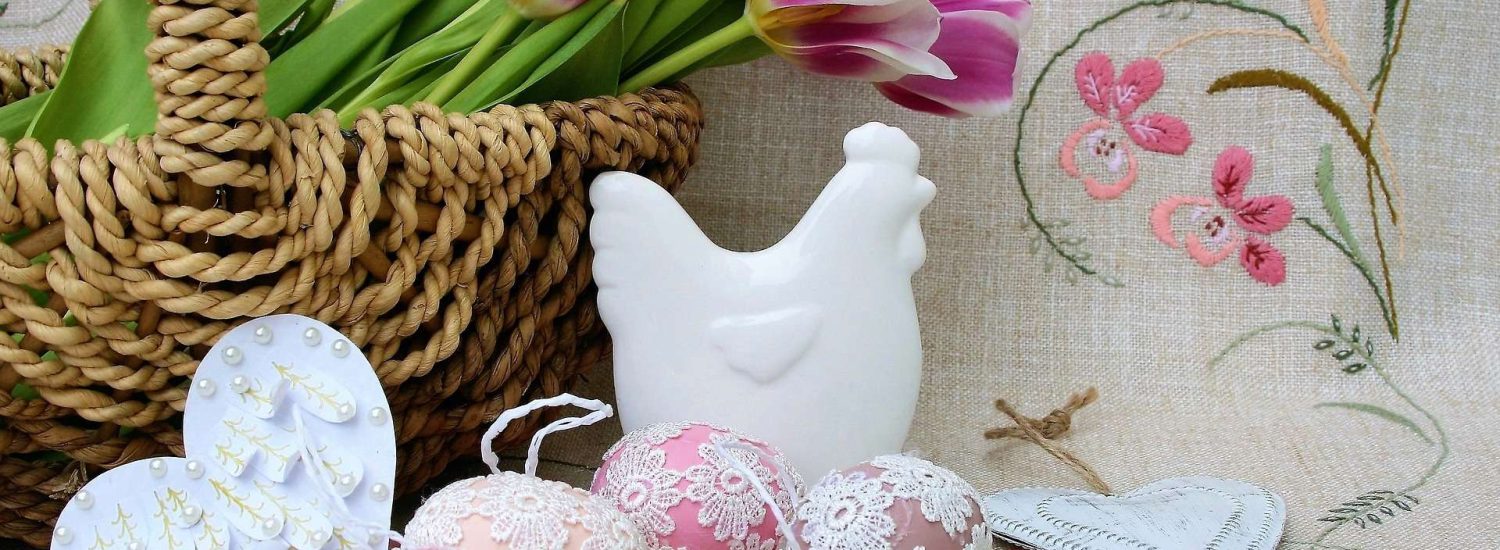
SME PRODUCTS INSPECTION
To encourage Small-Medium Entrepreneurs (SME), QIV offers exclusive and special inspection services for SME Manufacturers and also guides them on how to maintain the quality, knowledge shared on national & international regulations and requirements to export their products.
QIV provides quality services to SME manufacturers with significantly lower prices among South Asian Countries (India, Pakistan, Bangladesh, Nepal & Srilanka) which is USD 100 per Manday charge.
QIV inspection covers all kinds of SME & eco Products including the following;
- Jute Products
- Natural Leaf’s Products
- Sea Grass Products
- Clay Products
- Bamboo Products
- Candle Products
- Various Grass Products
- Handmade Textile Products
- Saree, Katha etc
- Other Handmade and small capacity manufacturing Products
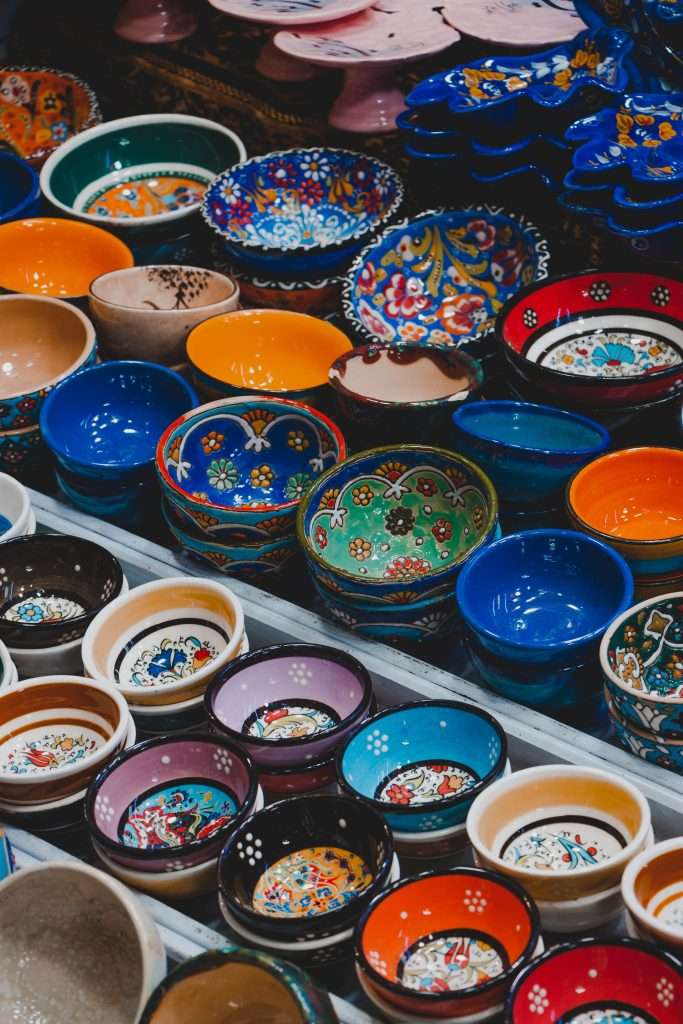
PPE INSPECTION
QIV Global Team is cable of doing inspection for all types of inspection on Medical and Safety related PPE like Mask, Safety googles, Hand Gloves, Gown.
Moreover, there are many countries have been introduced specific requirement on PPE Production as well as importing PPE. QIV offers quality inspection and verifications of manufacturing process, quantity, quality, measurement, defects, risk, regulations etc.
We convert your Pain Points to the Comfort Zone!
- Face all quality challenges in a common platform
- Standardization of quality matrix and
- Able to see the quality insight.
- Align with the shopper’s quality expectation
- Increase confidence of manufacturers
- Better quality products increase better business potentiality
- Better communication and understanding between suppliers and buyers
- Increase process efficiencies
- Through QIV factory evaluation, the buyer will be able to understand the performance of the supplier.
- Buyer can monitor the quality of every step of the production process through quality inspection by QIV.
- Supplier performance can be analyzed against styles, order etc.
- Better supplier selection.
- Trust and transparency.
- Better sourcing decisions
- Business Continuity and safety.
- Easy to take shipment decision
- Cost saving
- Control turnaround time from order management to reach the product in the shopping rack.
- Avoid product recall
- Better relations with the stakeholders
garment inspection
QIV conducts quality inspections at several stages of the manufacturing process to assure product quality. The inspection reduces the chance of product failure and minimizes order rejection due to faulty products, as well as an supply chain disturbance.
In order to inspect the goods, QIV normally follows international standards. However, we encourage client supplied protocols as well as any customized standards that clients may require.
QIV conducts inspections both online and on-site. However, upon mutual agreement, we can work on a man-day, man-month, or any other structure.
The is conducted before production starts at Supplier’s facility. It is usually done to crosscheck for final verification of bulk fabric, trims, raw materials/accessories, styling cutting way, cut, components, workmanship of the garment, pre-production sample, manufacturing details including production areas etc.
Our Inspectors will verify the availability and condition of materials, material’s in transition, review manufacturer’s plan for production and confirm equipment availability.
This inspection helps to ensure that supplier is ready to start production on time and meet the production deadlines. It also helps to identify any quality risks before commencement of mass production.
Key Checkpoints;
- Material conditions including ordered and received quantity.
- Conditions of bulk fabric, trims, raw materials/accessories, materials in transition, styling cutting way, cut, components, workmanship of the garment, pre-production sample, manufacturing details including production areas etc.
- Workmanship of materials and components
- Production readiness
- Equipment maintenance and availability
Fabric inspection is considered as pre- production inspection for garments or other textile products. It is very important to ensure the quantity and quality of the key materials of production like Fabric. This process is a preventive one that could be broadly defined as the process of determining if a product deviates from a given set of specifications.
It helps to identify the defects of fabrics to lower the risk of product rejection in later production stage. Generally, we use 4-point system to check fabric quality. QIV provide Fabric Inspection Services through visual, automated or online.
Quality inspection of garments or fabrics can be done by maintaining four systems. Although there are 4 methods of fabric inspection, but 4 point system is the most popular method to conduct fabric inspection.
Methods of the Fabric Inspections:
- 4 point system
- 10 point system
- Granville “78” System
- Dallas system
Inline Inspection is done at the start of production where a first batch of garments is inspected. It provides additional assurance of quality and provides a more transparent view of on-going production status by looking into the quality of semi-finished or final products and production lines.
It helps to take immediate action in possible discrepancies/variations and to make necessary corrections or adjustment to be made bulk production. IPI ensures better estimate the overall production and bring more improvement in the production with insightful Corrective Action Plans which developed by our experienced inspectors and endorsed by factory’s production experts.
QIV also recommend a follow up Inline Production Inspection is an ideal idea to ensure initial discrepancies have been corrected and rectified. This inspection is generally carried out when discrepancies have been detected during initial production inspection. However, this follow up is not necessary in case of having plan to conduct “During Production Inspection (DPI)”
Key Checkpoints;
- Bar Verifications
- Carton shipping mark Check
- Product packaging and packing Check.
- Product Assortment Check
- Color shade variation Check
- Rub Check by Water and Dry
- Product safety Check (Button, Zipper, Draw cord, Needle detection, Moisture GSM &Others)
- Product fitting Check (Measurement and Dummy)
During Production Inspection (DPI) is normally performed at 8 to 15 percent of the finished goods to ensure that any initial discrepancies/variations have been rectified. This inspection is a follow-up to the initial production check and ensure smooth production. Beside checking of the initial products coming off the line in a manner consistent with our pre-shipment inspection techniques, it also verifies and document the status of raw materials, components, and partially finished goods.
We use ANSI/ASQC Z1.4 (ISO 2859) to verify that your production run properly, you will be receiving your products as matching the samples you approved. Inspector will check the finished and semi-finished goods. Inspector will also point out possible defects during production. Our Inspection Report containing information about production flow, equipment use, production capacity and any potential issues in an easy format. This helps to find out possible defects and make rectifications at earlier production stage.
More DPIs can be conducted at different stages along the production period depending on complexity of products, production process, order quantity, reliability of the factory, etc.
Key Checkpoints;
- Initiated when the factory has manufactured 15 to 80 percent of the total order quantity
- Rigorous inspection of the initial finished product and raw materials, components and partially finished goods
- Gain early knowledge of potential quality issues
- Production status and capacity
- Workmanship
- Dimensions and weights
- On-site function and safety testing
When an order fails in pre-shipment inspection, defect sorting is sometimes used as a substitute for pre-shipment inspection of high-value products. Before shipment, QIV’s inspectors check the entire batch of finished goods according to your specified inspection check points. Then remove any defective goods from the production batch and either rework or destroy them, depending on the severity of the defect.
When quality issues are significant and rework is unfeasible, you may find yourself with a big number of goods that you can’t sell. Substandard items that you are unable to sell can harm your brand’s reputation in the long run. In such instances, QIV’s supervised product destruction may be your best option. We’ll coordinate destruction and oversee the destruction process to safeguard you and your customer.
QIV Production Monitoring will be your right choice if your supplier has failed several stage of inspections for the same reoccurring defects. This service enables you to significantly reduce the number of defective items that are packaged and dispatched. It will definitely save your time and money.
Pre-shipment inspections and production monitoring rarely take a random sample of a completed order. It helps to inspect the products at multiple stage on the assembly line until packaging. When inspectors identify defects, they remove the affected units from the line and segregate them for rework or other corrective action in accordance with your quality requirements.
Key Areas;
- Inspectors stationed on the factory floor throughout production to identify and communicate all defects found to your supplier
- Receive daily reports on order status and quality
- Assess progress on corrective actions
- Production line audit
- Workmanship
- Packaging and labeling
- Dimensions and weights
You might need to collect samples for review, evaluation, lab testing or just to make sure that your supplier correctly understands your requirements
The problem with asking your supplier to send you samples is that it’s hard to be sure the samples are representative. Often a supplier will choose only the best units or those they know will meet requirements. Later you might discover the quality, condition or characteristics of the finished goods you or your customers ultimately receive differ from the sample you collected earlier.
As a third-party independent company, QIV ensures a right sample selection process. Our Inspector will randomly pull samples in the factory. This assures that any sample testing or review results are representative and unbiased.
FRI is carried out when the production of the total quantity of an order or when at least 80% of your order has been export-packed. It’s designed to catch any quality issues with your finished products and packaging before they go into shipping containers. This stage will help you to make shipping decision.
Our inspector pulls a random sample of finished and packed goods, based on internationally recognized statistical random sampling technique AQL (ANSI / ASQ Z1.4-2003) along with industry-standard test results and measures and a percentage of the garments will be inspected.
This percentage usually being stipulated by your requirement. Our inspection verifies whether the material, performance, function, Quantity, workmanship, size specification, etc. and ensure the required product specifications are met as per your requirements or not.
Key Checkpoints;
- Initiated when the factory has manufactured 80 to 100 percent of the total order quantity
- Order quantity check
- Workmanship
- Dimension and weights
- On-site function and safety testing
- Packaging and labeling such as dirt & stains, the correct size of poly bag, garment quantity per carton, etc
- Shade variation from one part of the garment to another, correct labeling etc
Container Loading Supervision is final round inspection which ensures your order is completed and safely loaded in a container before shipment.
It protects you from theft, mishandling and incorrect loading. Our CLS services also cover quantity of goods to be loaded, cleanliness and environmental conditions of the containers will be checked. our inspectors will check packing details and quantity against documentation about at loading and will witness the whole process of loading the goods into the container.
This inspection may conduct in supplier’s factory premises or in the yard of shipping company.
Key Checkpoints;
- Initiated during loading of goods into shipping container
- Container conditions
- Product specifications
- Shipping marks, packaging and labeling
- Shipping documentation
- Quantity loaded
Mold is a fungus, and like all fungi, it thrives in moist places. Mold spreads by emitting spores, microscopic particles often as small as a single cell. Spores float around in the air until they land on a surface. Mold spores are everywhere, outdoors as well as inside your factory. It would be practically impossible to remove all mold spores from a factory without installing some kind of massive industrial clean room filtration system.
Luckily, mold spores only form mold when they land on a moist surface. That means that if you can keep the interior of your factory dry, you can avoid having any problems with mold. The best way to prevent mold in your home is to clean up spills, repair leaks in your roof, plumbing or HVAC system.
- QIV offers consultancy service for Amazon FB inspection process and preparation for conducting FB inspection by 3rd party inspectors who will inspect your goods on the spot before shipped to warehouse of Amazon.
- QIV will guide you about the specific requirements regarding product packaging, shipping packaging and labeling.
- QIV also offer self-reference inspection by quality inspectors who can check on site whether all of these are compliant with the guidelines and thus save possible fines and trouble with Amazon.
- Ensure to meet all quality expectations and applicable regulatory requirements & identify and remove the defective products from the production batch.
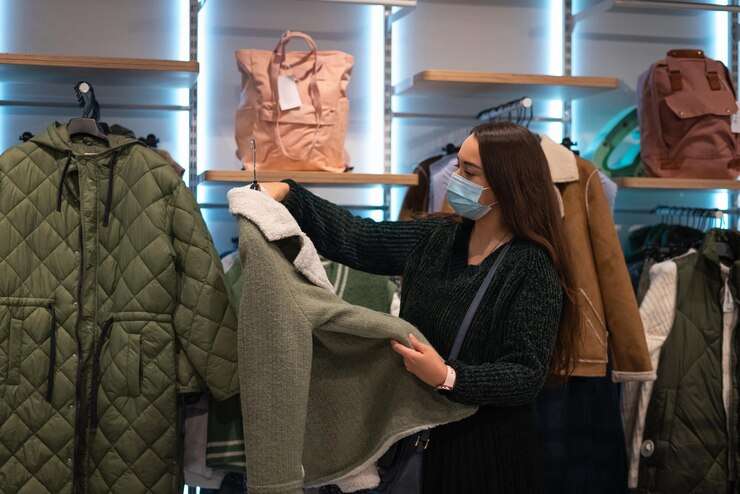