Leather and Footwear
QIV solutions enable retailers, brands and manufacturers of leather and footwear products to ensure the quality, safety and sustainability.
QIV Solutions enables to provide Inspections, fault diagnosis, sustainable and quality solutions, product & factory assessment and audit to make sure the quality and safety of your leather and footwear products including the below:
Winter and Rain Boots
Synthetic shoes
Safety and works shoes
Men, Women, Children and babies shoes
Men’s, women’s and children’s footwear
Bags and luggage
Athletic and sports shoes
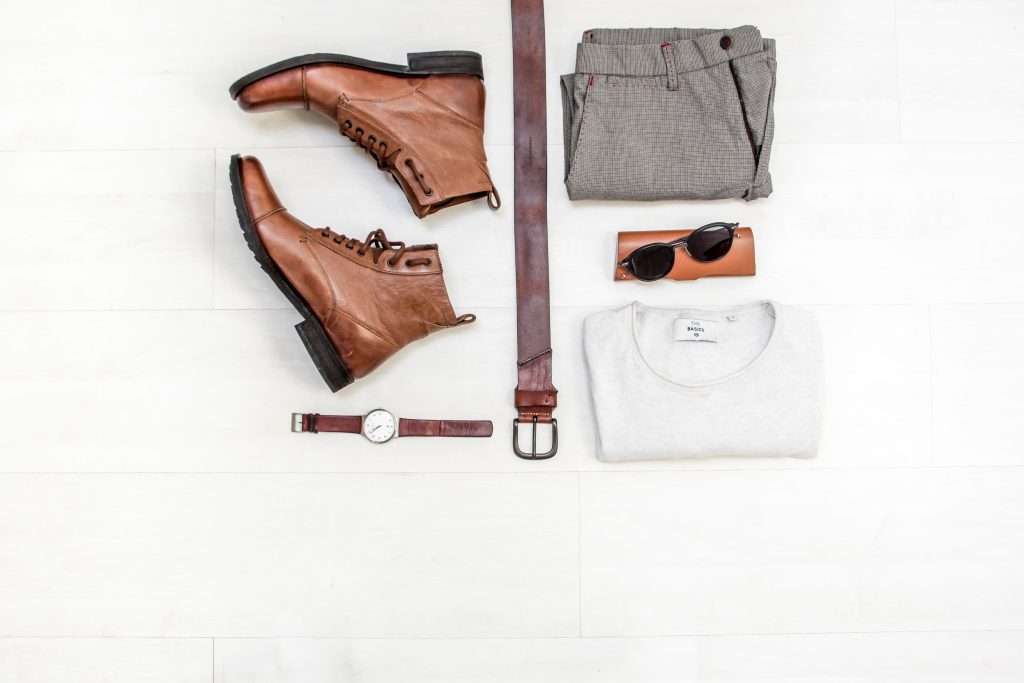
MANAGING QUALITY IN LEATHER & FOOTWEAR INDUSTRY
The quality of leather and footwear goods is an essential factor that can affect the reputation, brand image, and market competitiveness of a manufacturer. The following are some important aspects of quality in the leather and footwear industries:
Material Quality: The quality of raw materials, such as leather, suede, or other materials, is crucial to the quality of the finished product. The selection of high-quality materials ensures that the finished product will have the desired characteristics, such as durability, softness, and colorfastness.
Production Quality: The quality of production processes, including cutting, stitching, and finishing, determines the consistency and accuracy of the finished product. Strict quality control measures must be in place to ensure that each product meets the specified standards and requirements.
Design Quality: The quality of the design of leather and footwear products plays a significant role in their success in the market. Designs must be innovative, aesthetically pleasing, and functional.
Fit and Comfort: Footwear must fit well and be comfortable to wear. Poor fit and discomfort can lead to customer dissatisfaction and returns.
Durability and Longevity: Leather and footwear products must be durable and able to withstand wear and tear. They should also retain their shape and color after repeated use.
Safety and Regulatory Compliance: Leather and footwear products must meet safety and regulatory standards. For example, products must be free of hazardous materials and meet flammability standards.
Environmental and Social Responsibility: The leather and footwear industry is increasingly focused on environmental and social responsibility. Manufacturers are expected to implement sustainable practices and ensure that their products are produced under ethical working conditions.
Craftsmanship: Leather and footwear products require skilled craftsmanship to produce high-quality products. Experienced craftsmen can ensure that each product is made with attention to detail, resulting in a premium product that stands out in the market.
Testing and Quality Assurance: Testing is an essential aspect of quality control in the leather and footwear industries. Products should undergo rigorous testing for factors such as tensile strength, abrasion resistance, water resistance, and slip resistance. Manufacturers must also implement quality assurance measures to ensure that each product meets the required standards and specifications.
Supply Chain Management: Effective supply chain management is crucial for ensuring quality in the leather and footwear industries. Manufacturers must work closely with suppliers to ensure that raw materials meet the required quality standards. They must also maintain transparency throughout the supply chain to ensure that all parties comply with ethical and environmental standards.
Brand Reputation: Brand reputation is closely linked to product quality in the leather and footwear industries. Manufacturers with a reputation for producing high-quality products can charge premium prices and enjoy a loyal customer base. On the other hand, poor quality products can damage brand reputation and lead to loss of sales and customers.
After-Sales Support: Providing after-sales support is an important aspect of quality in the leather and footwear industries. Manufacturers must offer repair and replacement services for faulty products and ensure that customers are satisfied with their purchases. Good after-sales support can lead to increased customer satisfaction, loyalty, and positive word-of-mouth recommendations.
Continuous Improvement: Manufacturers must strive for continuous improvement in quality to remain competitive in the market. This involves regularly reviewing and refining production processes, incorporating new technologies, and incorporating customer feedback into product development.
Quality in the leather and footwear industries encompasses a range of factors, including material quality, production quality, design quality, fit and comfort, durability, safety and regulatory compliance, environmental and social responsibility, craftsmanship, testing and quality assurance, supply chain management, brand reputation, after-sales support, and continuous improvement. By prioritizing quality in all aspects of their operations, manufacturers can produce high-quality products, build a strong reputation, and remain competitive in the market.
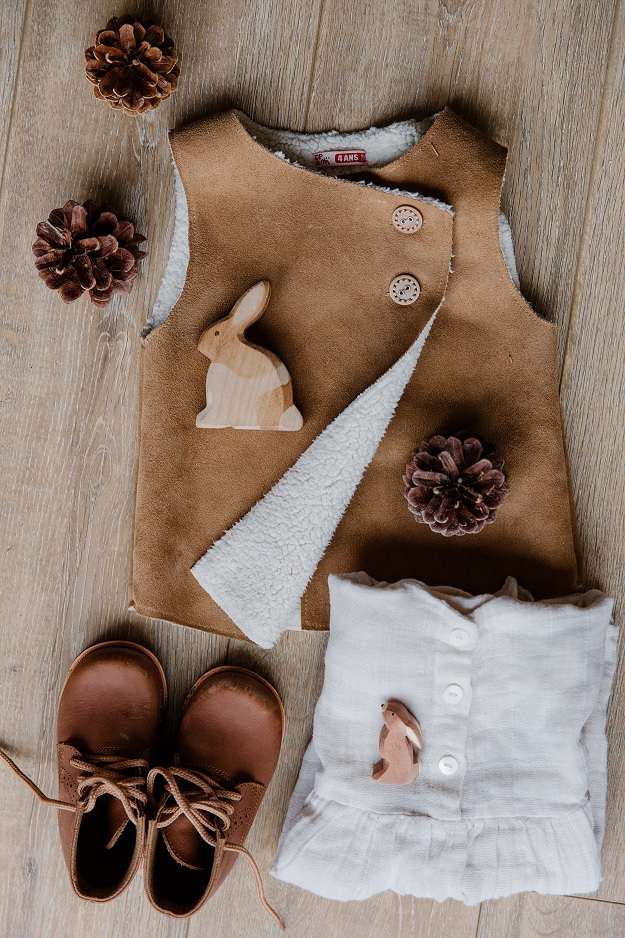

QUALITY INSPECTIONS IN LETHER & FOOTWEAR GOODS
Quality inspection is an important process in the leather and footwear industries, as it ensures that the finished products meet the required quality standards and specifications. Here are some steps involved in quality inspection in the leather and footwear industries:
Â
Incoming Material Inspection: The first step in quality inspection is to inspect the raw materials, such as leather, synthetic materials, or hardware components, before they are used in production. This helps to identify any defects or quality issues that may affect the finished product.
Â
In-Process Inspection: During production, inspectors should conduct regular inspections to ensure that the products are being made according to the required quality standards. This may include checking for consistency in product dimensions, ensuring that the stitching is tight and even, and verifying that the finishing is consistent.
Â
Final Product Inspection: Once production is complete, the finished products must undergo a final inspection. Inspectors should check for overall product quality, including fit, finish, stitching, and color consistency. They should also check that the products meet safety and regulatory requirements.
Â
Quality Control: The final step in quality inspection is to implement quality control measures to ensure that any defects or quality issues are identified and addressed before the products are shipped to customers. This may involve conducting spot checks or testing a sample of products to verify that they meet the required quality standards.
Â
Documentation and Reporting: Throughout the inspection process, it is important to maintain detailed records of the inspection results. This documentation helps to identify trends or issues that may require further attention and provides a record of quality compliance that can be shared with customers and stakeholders.